Breaking Fewer Eggs:
Reducing Conveyor Areas with High Risk of Mechanical Damage by 90%
Reducing Conveyor Areas with High Risk of Mechanical Damage by 90%
Using precise, real-time impact data on mechanical forces in their conveyor set-up, this major egg producer decreased impact-prone areas by 90%, protecting both their product and profits.
“CracklessEgg gave us clear visibility into problem areas, eliminating the need for guesswork. It was shocking to discover that 78% of our conveyor areas posed a risk of mechanical damage to our eggs. In just three weeks, we made a 90% improvement.”
Engineering Team Manager
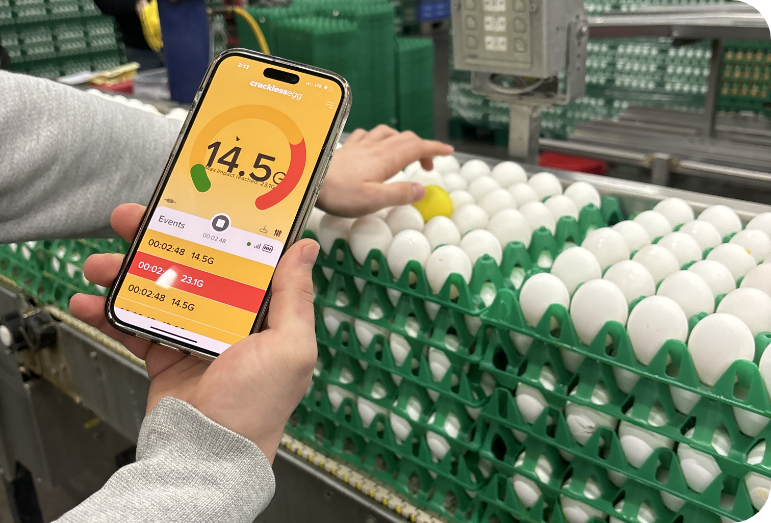
The Conveyor Challenge: Tackling Breakage and Micro-Fractures
One of the largest egg producers in the U.S. faced a significant challenge with excessive egg breakage along their complex conveyor lines and transfer points. Hidden micro-fractures—often invisible to the naked eye—posed a serious contamination risk, impacting both efficiency and safety.
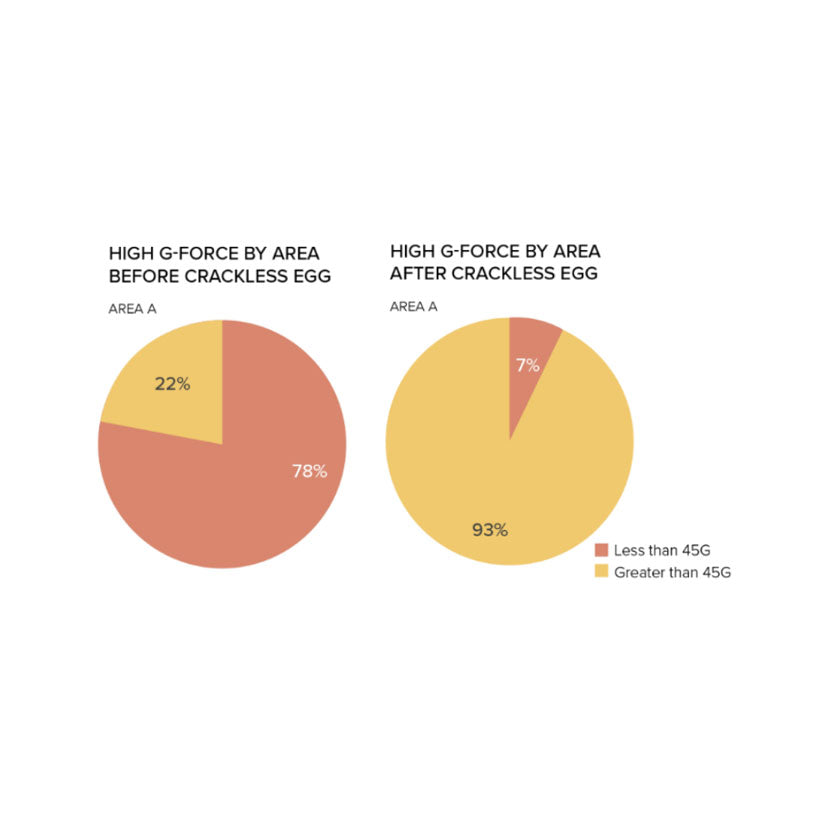
Adjustments Lead to 90% Reduction in High-Impact Areas
In just 3 weeks of using CracklessEgg, impact-prone conveyor areas over 45G were reduced from 78% to just 7%, significantly minimizing breakage. Adjustments to transfer points and conveyors were made in real time, leading to smoother, more efficient operations. The team was able to reduce downtime for cleanup and lower the risk of contamination, setting the stage for long-term operational improvements.